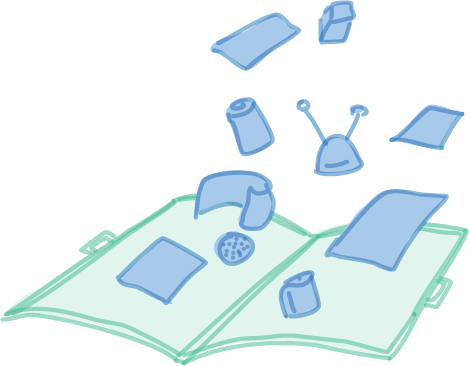
1. Give young people access to modern tools of production at an early age
Pittsburgh started out by placing a makerspace inside a single school. From this evolved something they call the “Dream Factory”: a set of integrated classrooms where young people learn how to use computers, 3D printers, and CNC tools to create robots, drones, et. al. This kind of education goes way beyond STEM to build the kind of problem solving skills to last a lifetime.
2. Leverage college and universities on a regional basis
Encouraging colleges to offer training in the modern tools of production (e.g. CNC tools, robotics); encourage universities to open up their facilities–particularly makerspaces–to residents. Case Western Reserve University did this to good effect, building a huge makerspace called think[box] and making it available to residents of Cleveland (OH). Beyond a makerspace, the major research universities are creating the IP that will drive the next set of industries. For example, Huntington (WV) in Appalachia is working with Marshall University to create a set of companies and jobs around advanced polymers.
3. Sit down with representatives of major corporations in your area
Understand their exact workforce requirements and align your high school(s) and/or community colleges. The Chicago city schools are doing this to good effect and it has been transformative.
4. Test drive new forms of workforce development to lift people into the middle class
We need workforce development that focuses on 1) understanding how to do business in the 21st century (for example: how to use crowdsourcing funding platforms) and 2) how to operate and master modern tools of production (3D printers, CNC tools, electronics, robots).
5. Look closely at your zoning
Makers need low-cost space to build initial prototypes and experiment. Live/work zoning can help. As Makers turn their prototypes into businesses and scale up, there is a need for low-cost space that starts small (500 square feet) and grows with the business. Think of the Brooklyn Navy Yard which took an unused shipyard and turned it into spaces for artists, artisans, Makers, and manufacturing. The Pratt Center has studied the success of the Brooklyn Navy Yard and created a practical tool kit designed to help other communities reclaim unused industrial space.
6. Avoid dead ending your economic development efforts
Cities like Fremont (CA) are reinventing themselves as advanced manufacturing centers through a combination of transit-friendly housing and zoning that encourages advanced manufacturing. Avoid chasing low-value manufacturing or distribution centers; the jobs here do not pay enough to lift people into the middle class and are ripe to be automated out of existence thanks to robots.
Another thing to avoid: focusing too much on downtown revitalization. The fastest growing cities and towns are those that think of themselves as a set of neighborhoods and invest on a neighborhood-by-neighborhood basis.
7. Make high-bandwidth internet available as low-cost, municipal service
Chattanooga (TN) and San Ramon (CA) did this to good effect. The benefits include: eliminating the homework divide by making internet affordable to low-income families, encouraging entrepreneurs and Makers to set up shop in your town. But beyond these immediate benefits, there is evidence that advanced manufacturing will require access to the internet at gigabit speeds.
8. Build preference for locally-made goods
Portland (OR) has done this to good effect with it’s Portland Made program.
9. Encourage a local supply chain to flourish
One way to do this is to analyze the industries you already have, figure out how resilient are the jobs in these industries, and double down on only a handful of industries that are most resilient to change. Not every city or town can be a Silicon Valley. That said, many cities and towns sit adjacent to major research universities, can benefit from the IP developed there, and can establish local supply chains. Albany, NY (nanotech) and Huntington, WV (advanced polymers) are examples of cities and towns that are thriving in this way.
10. Measure outcomes in terms of the number of resilient jobs created
Resilient jobs are jobs that take advantage of a local supply chain (at least 50% of the product is made locally), that pay at least $20/hour, where workers with different skills are paid more for those skills, and where the employer has some explicit focus on upskilling workers on an ongoing basis.
Praise for our Work
Press & Partners
How We Measure Results
The number of RESILIENT JOBS created
Join Our Mailing List
For monthly updates on projects and progress